Fiber
In the way of paper manufacture even is pulp or recycle paper used fiber. fiber or fibre are the slender, thread-like cellulose structures that forms the main part of tree trunk and from separated and suitably treated, cohere to form a sheet of paper.

Softwood Fiber
Internal Structure
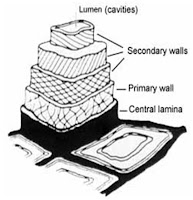
Fiber
study about fiber is closely related to the filler in papers and a variety of terms associated with the word. Below are some words related to fiber
- Fiber cut -----> A fiber cut is a short, straight cut located on the edge of the web, caused by a fiber embedded in the web of paper
- Fiber Coarseness -----> weight/unit lenght of fiber
- Fiber debris -----> Pieces of material which has been separated from the main body of the fiber
- Fiber flock -----> fiber that have agglomerated as a result of poor formation
- Fiber orientation-----> Refers to the alignment of the fibers in the sheet
- Fiberboard -----> Board made from defibrated wood chips, used as a building board
- Fibrillation -----> A structural change occurring in the wall of chemical fiber during beating
- Fibrils -----> String-like element that are loosened from the paper fiber during the beating process.They aid in the bonding processes when the paper is being manufactured
- Fiber axis Ratio -----> Ratio of fiber width to fiber thickness
Filler
Filler reduce strength properties of paper. Most of filler are cheaper than fibers and so filler are added to reduce the overall cost of paper.
Any inorganic substance added to the pulp during manufacturing of paper. Filler are also used to improve optical and other print-ability related properties. Filler improve opacity and brightness.
Test | Increased | Decreased |
Brightness | + | - |
Bursting Strength | - | - |
Caliper | - | + |
Dimensional Stability | + | - |
Folding Endurance | - | + |
Ink absorbency (Uncoated paper) | Gets more uniform | Gets less uniform |
Internal Bond Strength | - | + |
Opacity | + | - |
Picking Resistance | - | + |
Rattle | - | + |
Smoothness | + | - |
Stiffness | - | + |
Tearing Resistance | - | + |
Tensile Strength | - | + |
Fines
Small particles fiber defined arbitrarily by classification.